2016/06/20(月) - 09:49
スペイン・マドリード近郊にて行われたローターのプレス向けイベント。本ページでは、同社初ロード用フルコンポーネント「UNO」に続いて発表された新型パワーメーター「2INPOWER」を紹介。加えて本邦初公開のローター本社ファクトリー訪問の模様もお届けする。
ローターの新型クランク式パワーメーター 2INPOWER(中心部のシルバーのパーツは、製品版では赤アルマイトとなる)
2013年にパワーメーター界へと参入したローターは、これまでに「ROTOR POWER」「ROTOR POWER LT」「INPOWER」という3モデルをリリースしてきた。いずれのモデルも、クランクとしての高い基本性能に優れた計測精度、楕円チェーンリングと紐付いた独創的かつ実用的な機能を兼ね備え、多くのサイクリストから支持を獲得。これまでに14,000セット以上のセールスを記録し、パワーメーター界においても一大ブランドとなった。
2INPOWERを開発したエンジニアたち photo:ROTOR
2INPOWERを使用するマーク・カヴェンディッシュ(イギリス、ディメンションデータ) photo:Tim de Waeleこのように飛躍的な成長を遂げるローターにとって、4つめのパワーメーターとなるのが「2INPOWER(ツインパワーと読む)」である。機材フリークな方の中には既にご存知の方も多いと思われるが、1月のツアー・ダウンアンダーからディメンションデータが実戦テストを開始。マーク・カヴェンディッシュ(イギリス)やボアッソンハーゲン(ノルウェー)も常時使用しており、パワーメーターとしてもクランクとしても、その性能はお墨付きと言えよう。
設計ベースとなったのは、パワーを計測するひずみゲージをクランクアクスルに内蔵することで、優れた計測精度を実現した「INPOWER」。左側のパワーのみ計測する「INPOWER」に対し、製品名の通り「2INPOWER」は左右それぞれのパワーを計測することが特徴だ。ただし、「2INPOWER」は左右計測以外にも複数のメリットを有している。
「2INPOWER」に搭載されるひずみゲージの数は8つ。左側を計測する4つがアクスルに、右側を計測する4つが右クランクアームにそれぞれ内蔵される。この構造による最も大きなメリットは外気温の変化や変速ショックなどのノイズが計測データに影響しにくいこと。そして、転倒した際のダメージ、雨や泥による故障のリスクが少ないという点も「INPOWER」と同様だ。
設計のベースとなったのは、アルミクランクの3Dシリーズ
右アーム内には、4つのひずみゲージと、測定データを発信するためのアンテナが組み込まれている
アクスルには、左側のパワーを計測する4つのひずみゲージと、バッテリーが搭載される photo:ROTOR
中央部の黒いカバーを取り外すと充電ポートが表れる photo:ROTOR
ひずみゲージの内蔵に加えて、より高精度な計測を可能とするのが加速度センサーの搭載だ。トレーニングの指標となるワット数は「クランク軸に垂直な力」「角速度」「クランク長」の掛け算によって算出される。一般的に「角速度」はケイデンスセンサーで計測されるが、その場合の計測頻度はクランク1回転あたり1回もしくは2回となる。
右クランクの角度と左右合計出力の関係を表した「TORQUE 360°」。過去2回転分のパワーを計測データ(赤と青)や最大トルクを記録したクランク角(緑)が表示される image:ROTORしかし「角速度」はクランクが1回転する中でも変化しており、Q-Ringsを使用した場合には更に大きく変化する。ローターはこれに着目し、ケイデンスセンサーの代わりに「2INPOWER」には加速度センサーを搭載することで、クランク1回転あたりの角速度の計測回数を200回とした。
この緻密な計測をもとに、ローターの専用PCソフトウェアでは他に類を見ないほど詳細なペダリング分析を行うことができる。その中でも特に特徴的な分析が「TORQUE 360°」だ。これは、円グラフ上にペダリングパワーの大きさと方向(=トルク)を表示し、それをクランク1回転ごとにモニタリングできるというもの(円グラフの赤と青)。
また、同じ円グラフ上には、最もトルクが大きかったクランク角「OCa°(円グラフ中の緑の矢印)」が表示され、そこからQ-RingsやQ-XLの最適なセッティングを導き出すことができる。加えて左右のパワーバランスやTorque Effectiveness(総合トルクと正トルクの比率)、Pedal Smoothness(平均パワーと最大パワーの比率)の分析も可能だ。
重量は172.5mmサイズで645g。同等スペックのINPOWERに対して80gほどの重量増となるが、重量物はアクスル内に収まっていることから、重心を低く保つことができ、バイク全体の運動性能への影響は極めて少ない。ロード用とMTB用で複数のモデルが設定されるが、いずれもアクスル径は30mm。ローターのBB/ベアリングを用いることで、多種多様な規格のフレームに適合する(トレックの上位モデルに採用されるBB90は非対応)。
バッテリーは内蔵式で、MacBookのマグセーフの様な磁石付き専用コネクタを用いて充電を行う。フル充電までの時間は5時間で、ランタイムは250時間。INPOWERが300時間であることや、クランク1回転あたり200回の角速度計測を行うことを考慮すれば、非常にもちが良いといえるだろう。
通信規格はANT+に対応し、ガーミンEdgeを始めとしたパワー(W)を表示できるサイクルコンピューターを使用してデータの表示及び収集ができる。またBluetooth対応となったことで、パソコンやスマートフォンとの直接連携可能に(Bluetoothを用いてサイクルコンピューターと接続することはできない)。これまで収集したデータはパソコン用の専用ソフトウェアでのみ分析できたが、今後リリース予定のスマートフォン用アプリでも分析可能となる。
2INPOWERで紐解く勝利の理由
ティレーノ〜アドリアティコ第4ステージを制したスティーブ・クミングス(イギリス、ディメンションデータ photo:Tim de Waele
レース中におけるケイデンスの分布。6時間4分49秒におよぶレースの間、クミングスは21%にあたる1時間15分に渡ってペダリングを止めていた (c)trainingpeaks.com
レース中におけるワット数の分布。レース時間の25%にあたる1時間30分に渡って、クミングスのワット数は 50W以下だった (c)trainingpeaks.com2INPOWERの製品プレゼンテーションの最後に、2INPOWERを用いて測定した実際のレースデータが紹介された。解説を務めたのは、UCIワールドチームのディメンションデータに所属するスポーツサイエンティストのジョナサン・ベーカー氏(電話出演)。春先に行われたティレーノ〜アドリアティコより、第4ステージで逃げ切り優勝を飾ったスティーブ・クミングスのデータを例にとり、なぜ優勝できたのかを分析した(レースレポートはこちらから)。
まず最初にベーカー氏が紹介したのがケイデンスのデータ。驚くべきことに、6時間4分49秒におよぶレースの間、クミングスは21%にあたる1時間15分に渡ってペダリングを止めていたのだ。ワット数のデータにも同様の傾向を確認することができ、レース時間の25%にあたる1時間30分に渡って、クミングスのワット数は50W以下だった。
長い下りが多ければペダリングを止める時間や、ワット数が低い時間が増えるのは当然だが、この日用意されたのは小高い山々を越えるアップダウンに富んだ中級山岳コース。ベイカー氏は「クミングスが如何に脚を貯めて、勝負どころへ備えていたかが分かる」とコメントしている。
残り3.6kmでアタックしたスティーブ・クミングス(イギリス、ディメンションデータ photo:Tim de Waele
アタックしてからフィニッシュするまでの3.6kmのデータ。アタックの後に4回の大きな加速を行い、3分46秒間の平均ワット数は451Wにも達した (c)trainingpeaks.com
左右のペダリングバランスの分布。平均は平均は49.7% / 50.3%をマーク
セーブした体力は勝負どころで遺憾なく発揮されることに。レース最初の2/3と、フィニッシュまでの1/3のデータを比較すると、平均ワット数は36%、平均心拍数とカロリー消費量は30%も上昇。残り3.6kmでアタックして独走に持ち込んでからフィニッシュするまでの3分46秒の間に加速を4回繰り返し、平均ワット数451Wで逃げ切ることに成功したのだ。
そして極限状態でレースを進めながらも、自らのパワーを効率良く推進力へ変換することも怠らないクミングス。レース中におけるペダリングの左右バランスの平均は49.7% / 50.3%をマーク。全データをプロットしたグラフは、左右どちらかに偏ること無く、正規分布を描いている。「この優れたペダリングスキルはトラックレースで培ったものだろう」とベイカー氏は解説を締めくくった。
マドリード近郊にあるローターの本社屋
スペインの玄関口の1つであるマドリード=バラハス空港から、高速に乗って車で30分ほど。スペイン国立航空宇宙技術研究所をはじめ、多くの研究開発施設や工場が軒を連ねるトレホン・デ・アルドスという地域の中にローターの本社と工場はある。なお、本社と工場は別々の建物に入っている。
スペインの乾いた雰囲気にマッチするブラウンの建物がローターの本社だ。玄関には、廃材を使って心臓を表現した「HEARTMADE」というオブジェが飾られており、来訪者を出迎えてくれる。本社屋は3階建てで、各所にはローターの製品を使うプロライダーの写真や、ビッグレースでの勝利を記念して作成されたスペシャルパーツが展示されているのだ。
ローターの心臓とも言うべき、玄関に飾られたオブジェ
3大ツール全てで、ローターのプロダクトは総合優勝に貢献した
グランツール制覇を記念して製造されたスペシャルカラーの3Dクランク
広々としたオフィス内
本社には、ローターの中核を担う設計開発部門や、世界各国に自社製品をPRするプロモーション部門、各プロダクトの組立部門、全世界へ製品をデリバリーする配送部門などが置かれている。本社の中には沢山の自転車が置かれており、その中にはプロトタイプを装着したものも。多くのスタッフがサイクリストであり、自らもパーツのテストを行っているという。
そして、ローターの各プロダクトが製造される工場は、本社屋の目の前に位置する。いかにも工場というギザギザとした屋根が特徴的だ。建物の前に秩序なく並べられた従業員の車がとてもスペインっぽいところ。建物の内部では、数十台のCNCマシンを始め、コンピューター制御された工作機械が大きな音をたてて稼働している。中には日本のDMG森精機の工作機械も活躍している。
ローターの全プロダクトが生み出される工場
工場内では様々な工作機械が稼働中 photo:ROTOR
この工場で消費されるアルミの量は年間202トン。この中で製品となるのが15%。残りの85%は切りくずとしてリサイクルに回されるのだそう。あまり歩留まりが良いとは思えないが「切削加工を多用することで得られるメリットを得ることができる」と、エンジニアのダヴィッド・マルティネス氏は言う。
まず、ローターのアイコンであるQ-Ringsやチェーンリングの製造過程を説明しよう。素材となるアルミ板は、1000mmx2000mmという大きな状態で素材メーカーから納入される。なお、アルミの合金種は製品にも記されているように7075T6としている。
チェーリングの製造は、ウォーターカッターを用いて円盤を切り出すところから始まる photo:ROTOR
治具を交換するマシン。コンピューターで制御されている photo:ROTOR
チェーンリングのバリエーションごとに用意される治具の数々 photo:ROTOR
多くの工程が自動で行われるが、バリ取りなどは人の手で行われる photo:ROTOR
品質検査にかけられるチェーンリング photo:ROTOR
完成したQ-Rings photo:ROTOR
納入された素材は、ウォーターカッターを用いて円盤状に切り出される。ウォーターカッターを使うのは、板が波打ってしまわないようにするためだという。切りだされた円盤は、治具に固定するための穴を開けて、CNCマシンの中へ。CNCマシンは、複数のサイズの刃物を取っ替え引っ替え交換しながら円盤を削り、刃先や肉抜き部、無数の取り付け穴を形作っていく。切削工程が終了したチェーンリングは、バリ取りを行ったあとに品質検査と塗装を経て完成となる。
次はクランクについて。クランクアームは意外なことにアルミ丸棒から切削されている。素材メーカーから納入された長い丸棒は所要の長さにカットされ、CNCマシンにセットされ、軽量化のために3本の長穴が開けられる。この後、別のCNCマシンにセットされて切削され、製品の形に。砥石で磨いた後に、製品によっては表面に高速の微粒子を当てることで表面の硬度を高めるショットピーニング加工を施し、塗装や品質管理の最終工程へ送られる。
意外なことに、クランクアームは丸棒から削りだされる photo:ROTOR
削りだされたクランクアーム photo:ROTOR
クランクアームには3つの長穴を開けることで、軽量化を図っている photo:ROTOR
パワーメーターの発信機を接着する photo:ROTOR
スパイダー部の工程も大まかな流れは共通。最後に、スピンドルを合わせた3点を組み立てることで、クランクは完成となる。なおアーム、スパイダー、スピンドルの3点はそれぞれ適材適所で合金種が変更されており、7075や6066などを組み合わせている。
UNOのカーボンレバーは、素材に熱可塑性カーボンを採用する photo:ROTORこの他、今回のファクトリービジットで見ることができたのが、UNOのブレーキレバーの製造工程だ。素材に、熱を与えると軟化する熱可塑性カーボンを採用することが特徴だ(フレームやホイールのカーボンは、熱を与えることで硬化する)。
この熱可塑性カーボンを数枚重ねたものを120℃に熱し、150Barもの高い圧力で型に押し当てることでUNOのブレーキレバーは成型されている。素材の質感を見るに恐らく、UNOのリアディレーラーもプーリーゲージと同じ製法で成型されているようだ。
こうしてスペイン・マドリードで製造され、日本を始めとした世界38カ国に届けられるローターのプロダクツ。Q-Ringsや3Dクランク、UNOが如何にして生み出されるかを、読者の皆さんが少しでも理解して頂き、これまでより少しでも興味が沸いたなら幸いである。
左右それぞれの出力を計測する新型クランク式パワーメーター「2INPOWER」登場
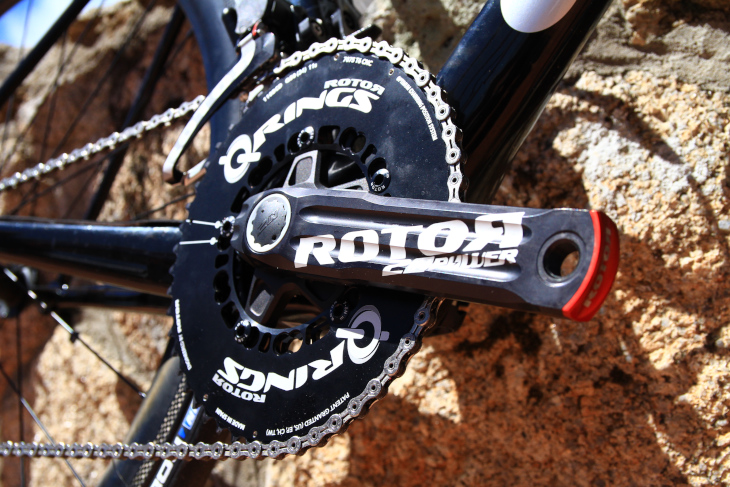
2013年にパワーメーター界へと参入したローターは、これまでに「ROTOR POWER」「ROTOR POWER LT」「INPOWER」という3モデルをリリースしてきた。いずれのモデルも、クランクとしての高い基本性能に優れた計測精度、楕円チェーンリングと紐付いた独創的かつ実用的な機能を兼ね備え、多くのサイクリストから支持を獲得。これまでに14,000セット以上のセールスを記録し、パワーメーター界においても一大ブランドとなった。
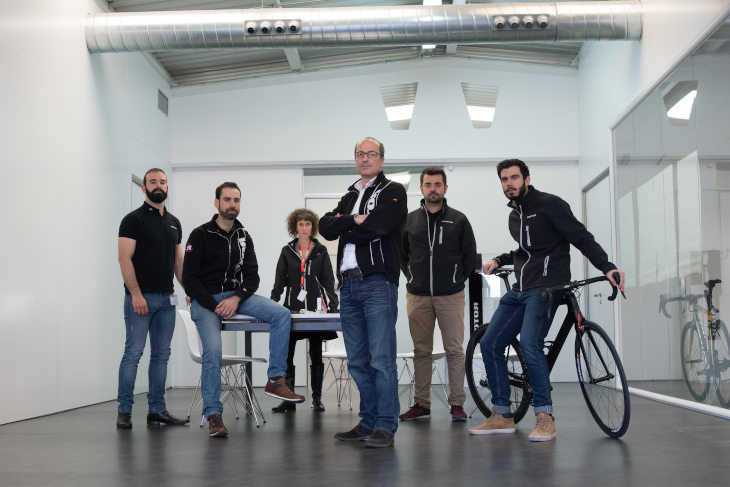
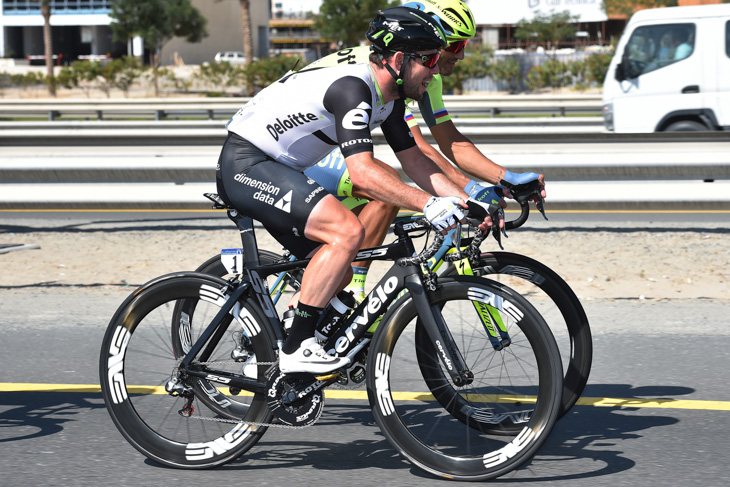
設計ベースとなったのは、パワーを計測するひずみゲージをクランクアクスルに内蔵することで、優れた計測精度を実現した「INPOWER」。左側のパワーのみ計測する「INPOWER」に対し、製品名の通り「2INPOWER」は左右それぞれのパワーを計測することが特徴だ。ただし、「2INPOWER」は左右計測以外にも複数のメリットを有している。
「2INPOWER」に搭載されるひずみゲージの数は8つ。左側を計測する4つがアクスルに、右側を計測する4つが右クランクアームにそれぞれ内蔵される。この構造による最も大きなメリットは外気温の変化や変速ショックなどのノイズが計測データに影響しにくいこと。そして、転倒した際のダメージ、雨や泥による故障のリスクが少ないという点も「INPOWER」と同様だ。
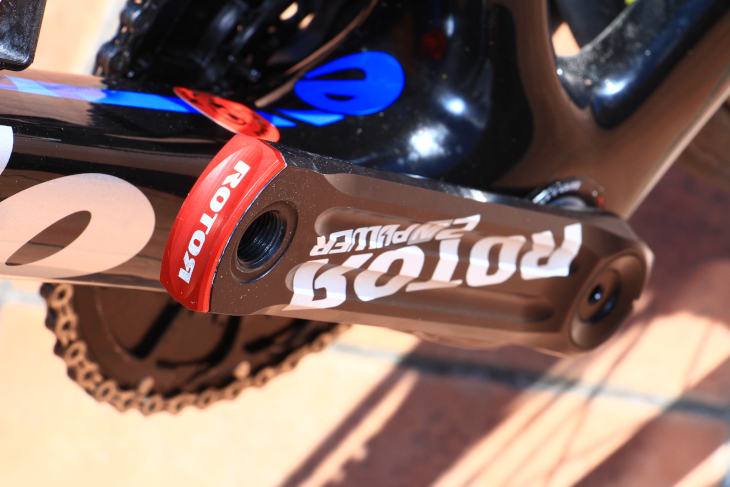
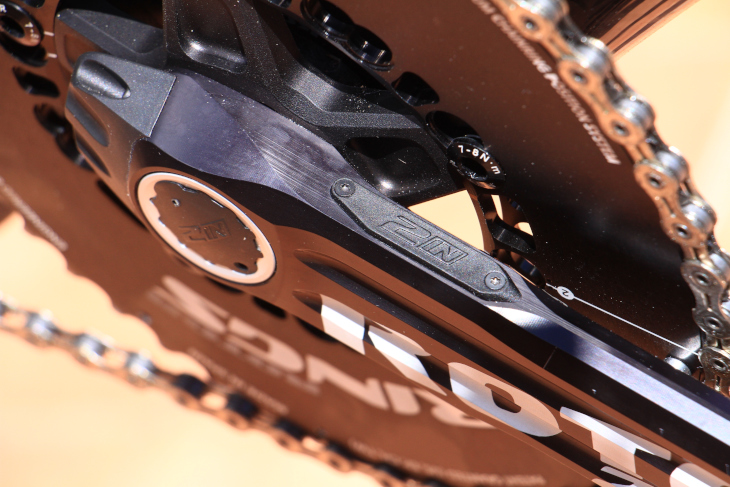
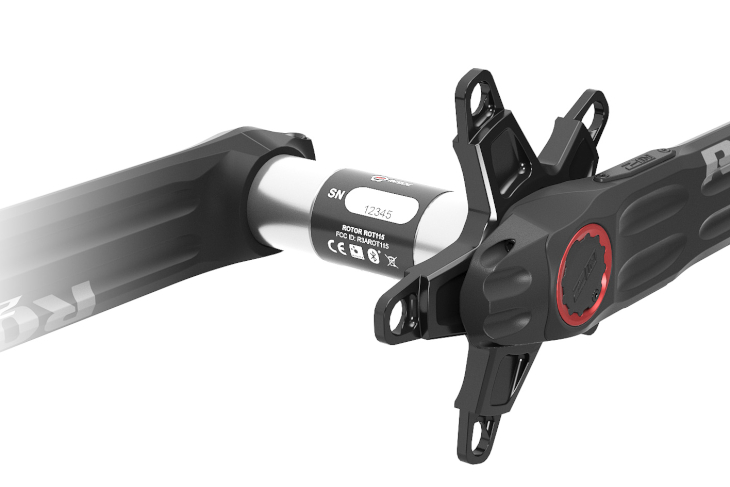
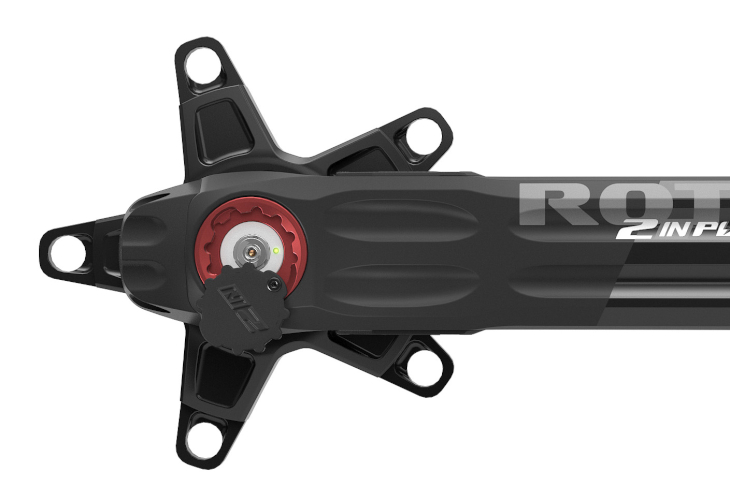
ひずみゲージの内蔵に加えて、より高精度な計測を可能とするのが加速度センサーの搭載だ。トレーニングの指標となるワット数は「クランク軸に垂直な力」「角速度」「クランク長」の掛け算によって算出される。一般的に「角速度」はケイデンスセンサーで計測されるが、その場合の計測頻度はクランク1回転あたり1回もしくは2回となる。
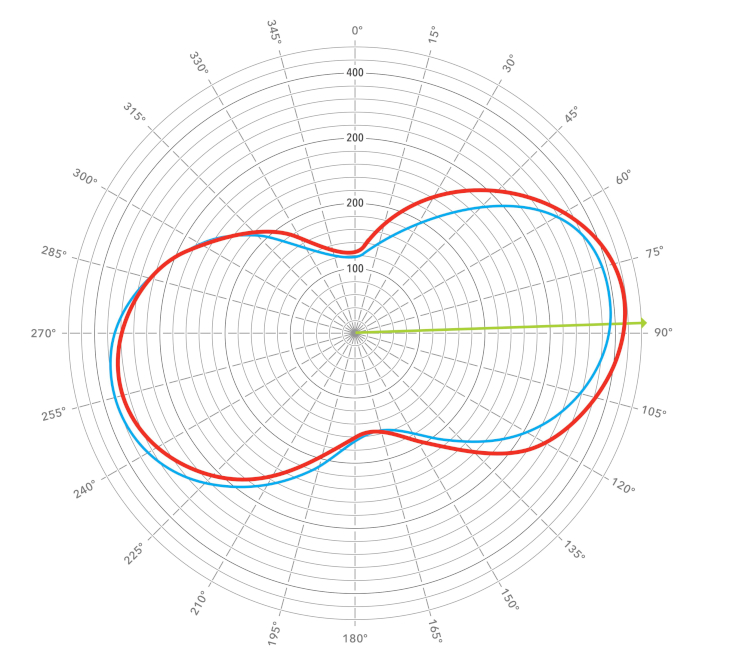
この緻密な計測をもとに、ローターの専用PCソフトウェアでは他に類を見ないほど詳細なペダリング分析を行うことができる。その中でも特に特徴的な分析が「TORQUE 360°」だ。これは、円グラフ上にペダリングパワーの大きさと方向(=トルク)を表示し、それをクランク1回転ごとにモニタリングできるというもの(円グラフの赤と青)。
また、同じ円グラフ上には、最もトルクが大きかったクランク角「OCa°(円グラフ中の緑の矢印)」が表示され、そこからQ-RingsやQ-XLの最適なセッティングを導き出すことができる。加えて左右のパワーバランスやTorque Effectiveness(総合トルクと正トルクの比率)、Pedal Smoothness(平均パワーと最大パワーの比率)の分析も可能だ。
重量は172.5mmサイズで645g。同等スペックのINPOWERに対して80gほどの重量増となるが、重量物はアクスル内に収まっていることから、重心を低く保つことができ、バイク全体の運動性能への影響は極めて少ない。ロード用とMTB用で複数のモデルが設定されるが、いずれもアクスル径は30mm。ローターのBB/ベアリングを用いることで、多種多様な規格のフレームに適合する(トレックの上位モデルに採用されるBB90は非対応)。
バッテリーは内蔵式で、MacBookのマグセーフの様な磁石付き専用コネクタを用いて充電を行う。フル充電までの時間は5時間で、ランタイムは250時間。INPOWERが300時間であることや、クランク1回転あたり200回の角速度計測を行うことを考慮すれば、非常にもちが良いといえるだろう。
通信規格はANT+に対応し、ガーミンEdgeを始めとしたパワー(W)を表示できるサイクルコンピューターを使用してデータの表示及び収集ができる。またBluetooth対応となったことで、パソコンやスマートフォンとの直接連携可能に(Bluetoothを用いてサイクルコンピューターと接続することはできない)。これまで収集したデータはパソコン用の専用ソフトウェアでのみ分析できたが、今後リリース予定のスマートフォン用アプリでも分析可能となる。
2INPOWERで紐解く勝利の理由
~クミングスのティレーノ〜アドリアティコ第4ステージ優勝を例に~
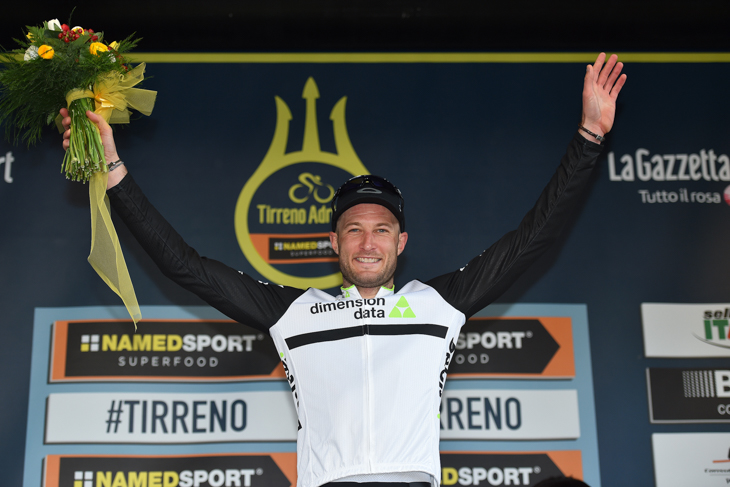
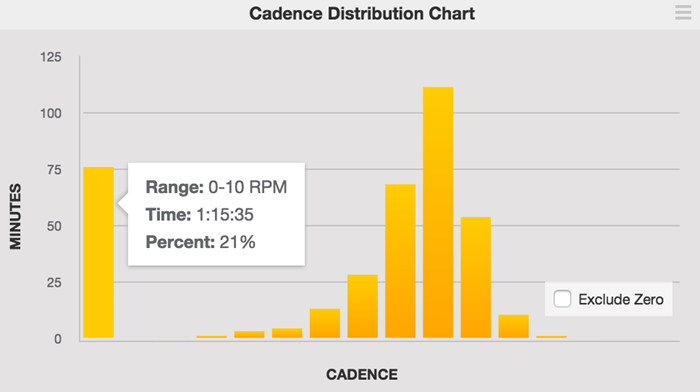
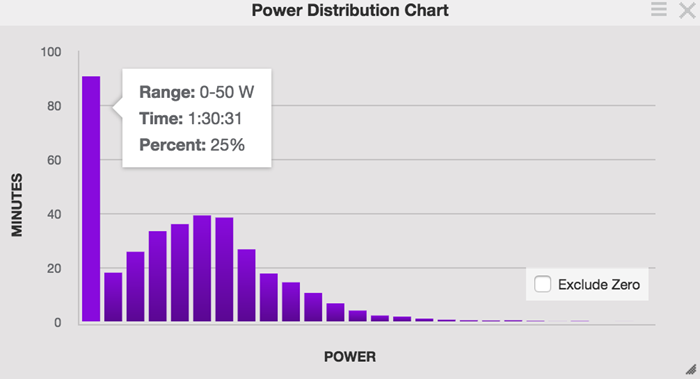
まず最初にベーカー氏が紹介したのがケイデンスのデータ。驚くべきことに、6時間4分49秒におよぶレースの間、クミングスは21%にあたる1時間15分に渡ってペダリングを止めていたのだ。ワット数のデータにも同様の傾向を確認することができ、レース時間の25%にあたる1時間30分に渡って、クミングスのワット数は50W以下だった。
長い下りが多ければペダリングを止める時間や、ワット数が低い時間が増えるのは当然だが、この日用意されたのは小高い山々を越えるアップダウンに富んだ中級山岳コース。ベイカー氏は「クミングスが如何に脚を貯めて、勝負どころへ備えていたかが分かる」とコメントしている。
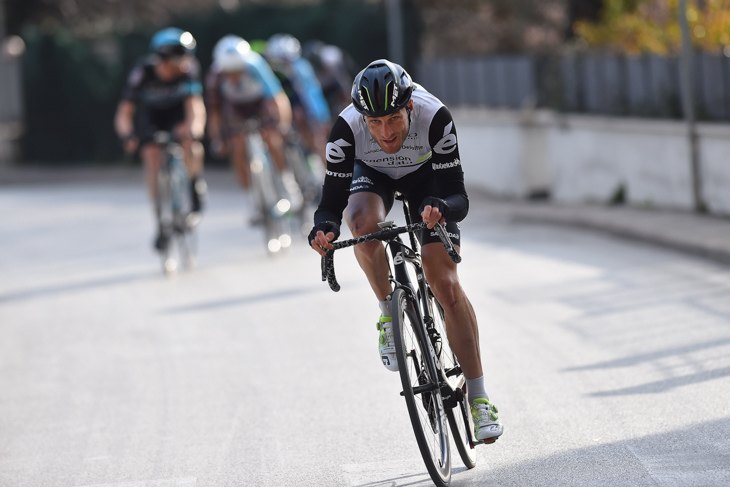
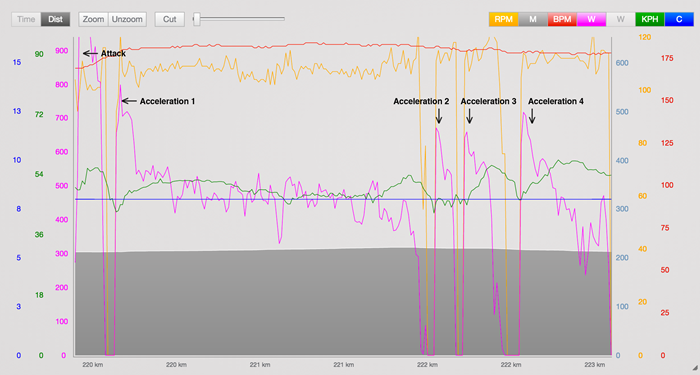
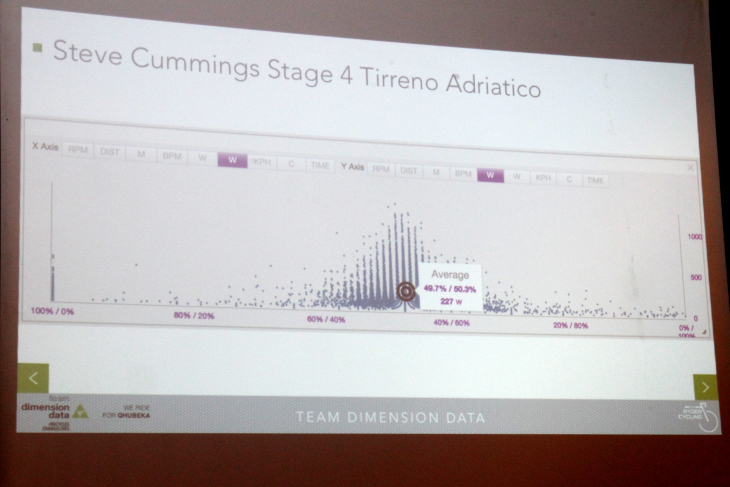
セーブした体力は勝負どころで遺憾なく発揮されることに。レース最初の2/3と、フィニッシュまでの1/3のデータを比較すると、平均ワット数は36%、平均心拍数とカロリー消費量は30%も上昇。残り3.6kmでアタックして独走に持ち込んでからフィニッシュするまでの3分46秒の間に加速を4回繰り返し、平均ワット数451Wで逃げ切ることに成功したのだ。
そして極限状態でレースを進めながらも、自らのパワーを効率良く推進力へ変換することも怠らないクミングス。レース中におけるペダリングの左右バランスの平均は49.7% / 50.3%をマーク。全データをプロットしたグラフは、左右どちらかに偏ること無く、正規分布を描いている。「この優れたペダリングスキルはトラックレースで培ったものだろう」とベイカー氏は解説を締めくくった。
ローターの全てが生み出される場所 マドリードの本拠地を訪ねる
このコンテンツの最後に、ローターのマドリード本社にて行われたファクトリービジットの模様をレポート。同社初のフルコンポーネントUNOや楕円チェーンリングQ-Rings、アルミクランク3Dシリーズ、パワーメーターといったローターの全ての製品が生み出される場所を紹介していく。(工場内では撮影が禁止されていたため、製造過程の写真はローター本社から提供されたものを使用した)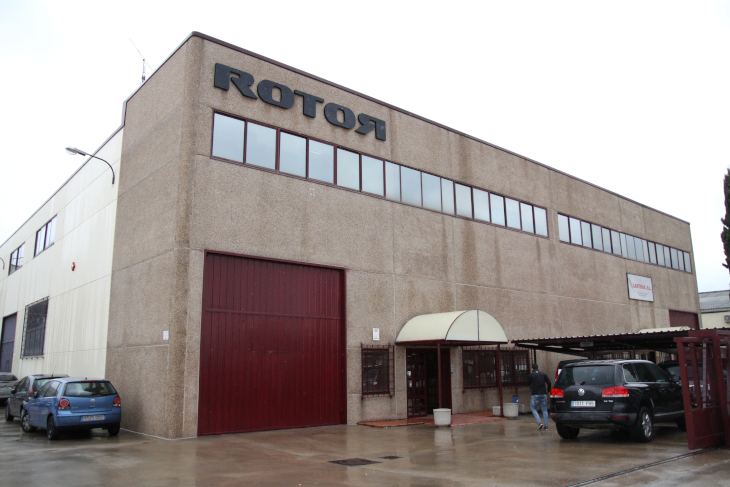
スペインの玄関口の1つであるマドリード=バラハス空港から、高速に乗って車で30分ほど。スペイン国立航空宇宙技術研究所をはじめ、多くの研究開発施設や工場が軒を連ねるトレホン・デ・アルドスという地域の中にローターの本社と工場はある。なお、本社と工場は別々の建物に入っている。
スペインの乾いた雰囲気にマッチするブラウンの建物がローターの本社だ。玄関には、廃材を使って心臓を表現した「HEARTMADE」というオブジェが飾られており、来訪者を出迎えてくれる。本社屋は3階建てで、各所にはローターの製品を使うプロライダーの写真や、ビッグレースでの勝利を記念して作成されたスペシャルパーツが展示されているのだ。
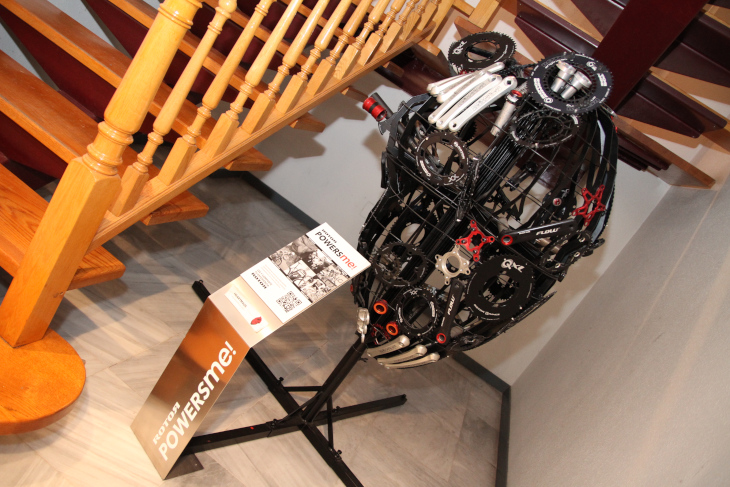
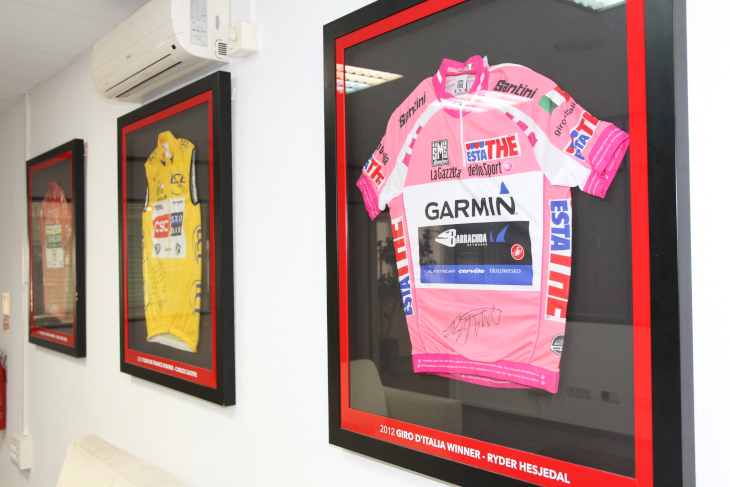
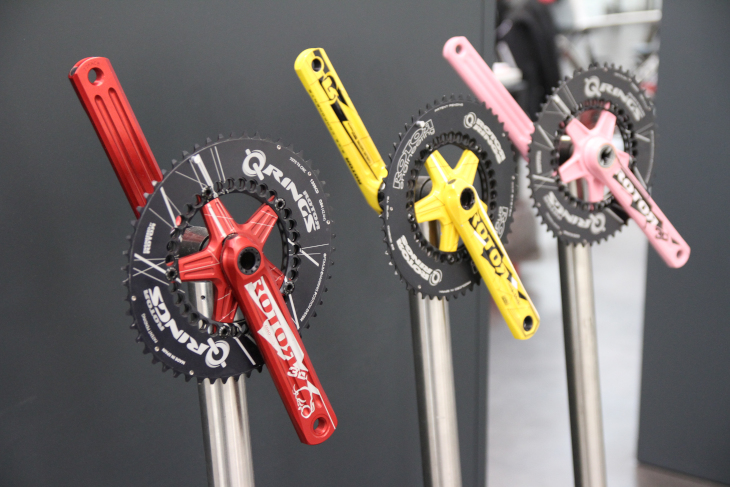
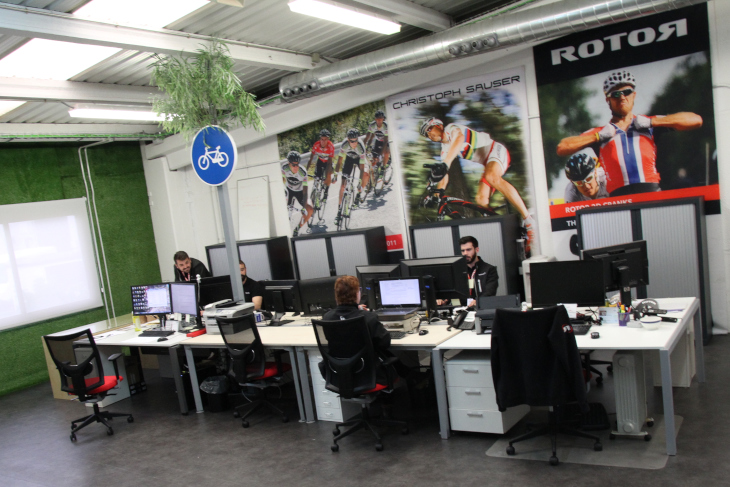
本社には、ローターの中核を担う設計開発部門や、世界各国に自社製品をPRするプロモーション部門、各プロダクトの組立部門、全世界へ製品をデリバリーする配送部門などが置かれている。本社の中には沢山の自転車が置かれており、その中にはプロトタイプを装着したものも。多くのスタッフがサイクリストであり、自らもパーツのテストを行っているという。
そして、ローターの各プロダクトが製造される工場は、本社屋の目の前に位置する。いかにも工場というギザギザとした屋根が特徴的だ。建物の前に秩序なく並べられた従業員の車がとてもスペインっぽいところ。建物の内部では、数十台のCNCマシンを始め、コンピューター制御された工作機械が大きな音をたてて稼働している。中には日本のDMG森精機の工作機械も活躍している。
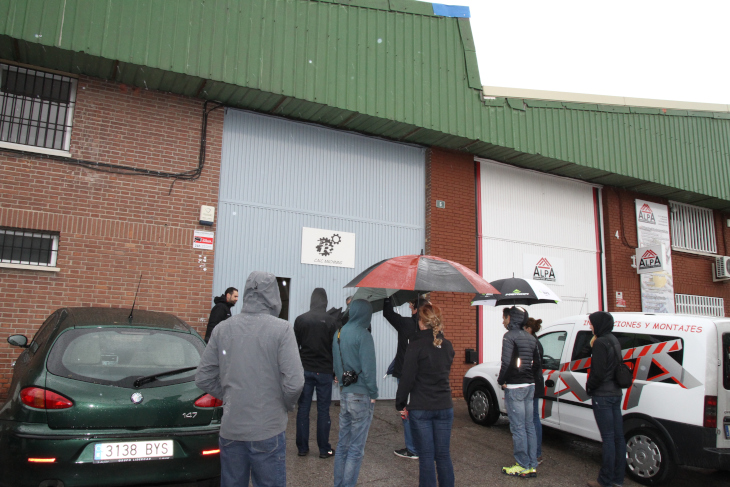
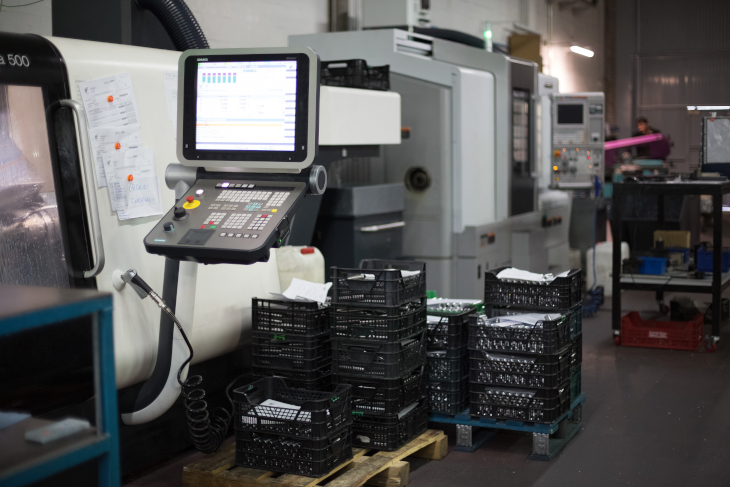
この工場で消費されるアルミの量は年間202トン。この中で製品となるのが15%。残りの85%は切りくずとしてリサイクルに回されるのだそう。あまり歩留まりが良いとは思えないが「切削加工を多用することで得られるメリットを得ることができる」と、エンジニアのダヴィッド・マルティネス氏は言う。
まず、ローターのアイコンであるQ-Ringsやチェーンリングの製造過程を説明しよう。素材となるアルミ板は、1000mmx2000mmという大きな状態で素材メーカーから納入される。なお、アルミの合金種は製品にも記されているように7075T6としている。
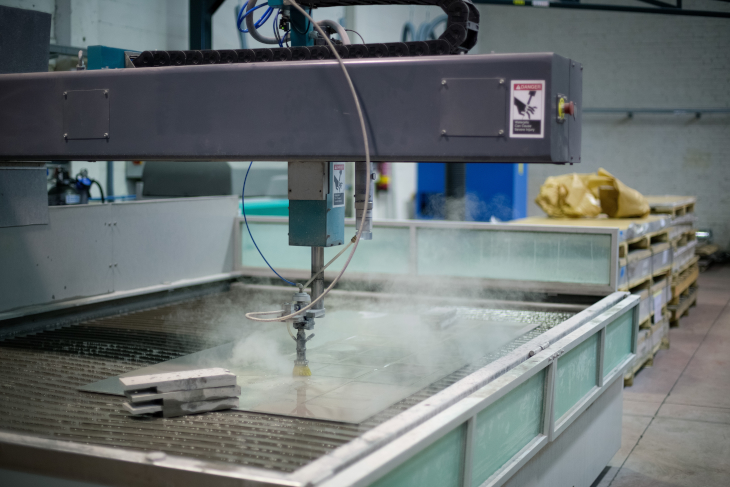
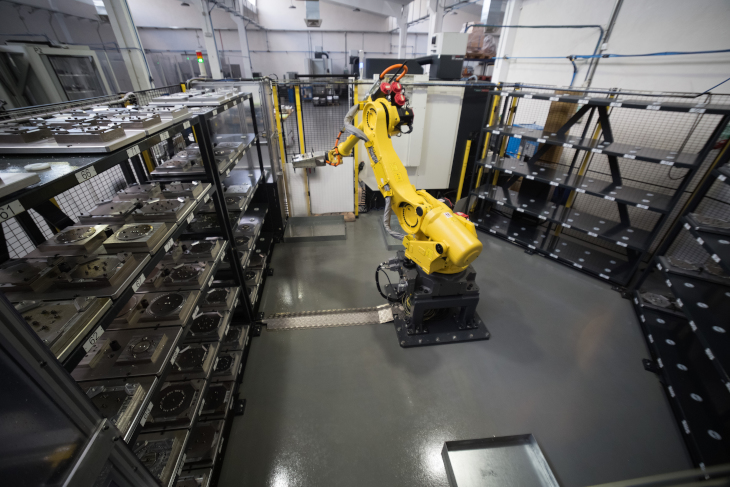
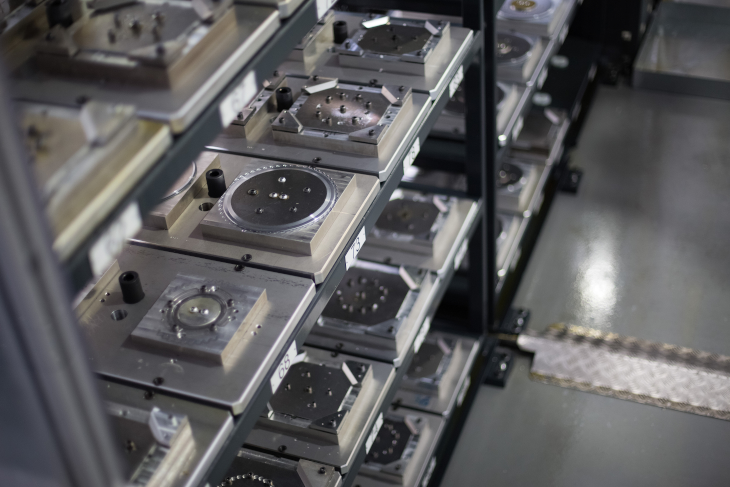
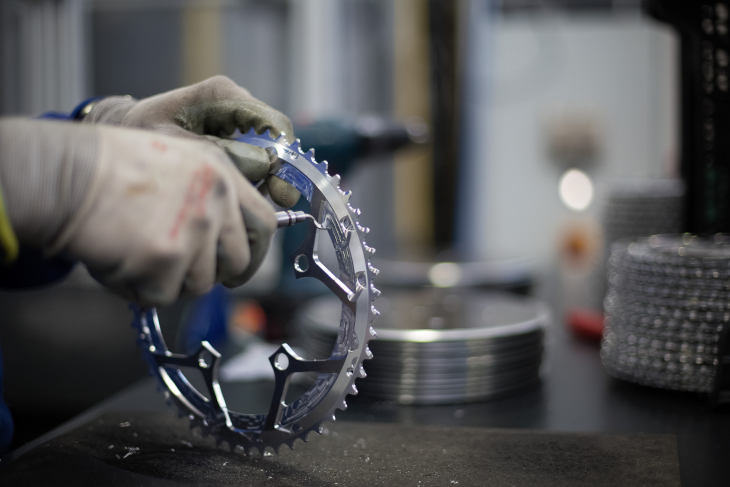
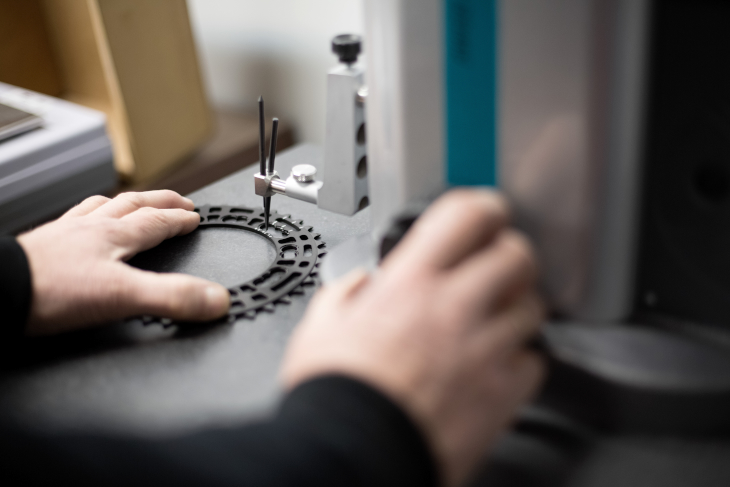
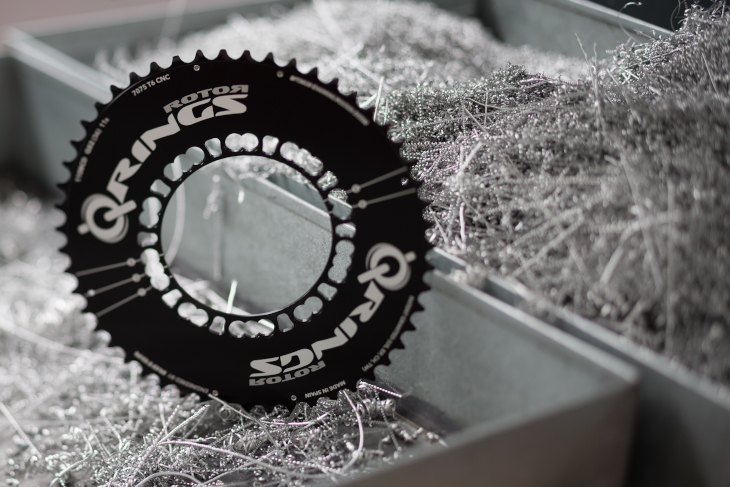
納入された素材は、ウォーターカッターを用いて円盤状に切り出される。ウォーターカッターを使うのは、板が波打ってしまわないようにするためだという。切りだされた円盤は、治具に固定するための穴を開けて、CNCマシンの中へ。CNCマシンは、複数のサイズの刃物を取っ替え引っ替え交換しながら円盤を削り、刃先や肉抜き部、無数の取り付け穴を形作っていく。切削工程が終了したチェーンリングは、バリ取りを行ったあとに品質検査と塗装を経て完成となる。
次はクランクについて。クランクアームは意外なことにアルミ丸棒から切削されている。素材メーカーから納入された長い丸棒は所要の長さにカットされ、CNCマシンにセットされ、軽量化のために3本の長穴が開けられる。この後、別のCNCマシンにセットされて切削され、製品の形に。砥石で磨いた後に、製品によっては表面に高速の微粒子を当てることで表面の硬度を高めるショットピーニング加工を施し、塗装や品質管理の最終工程へ送られる。
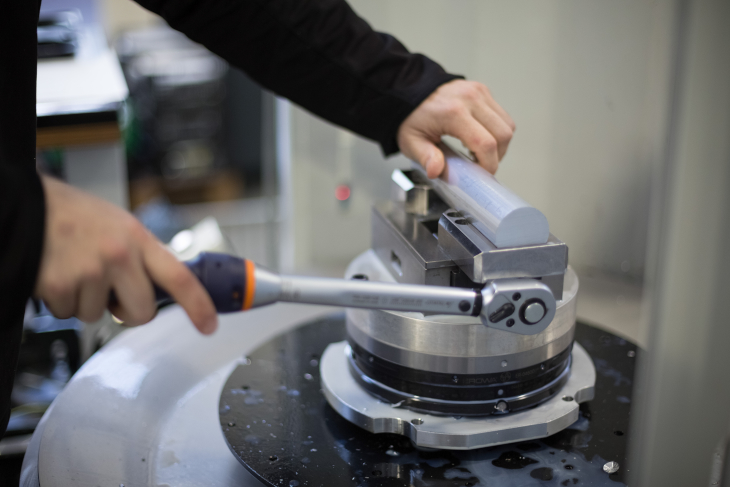
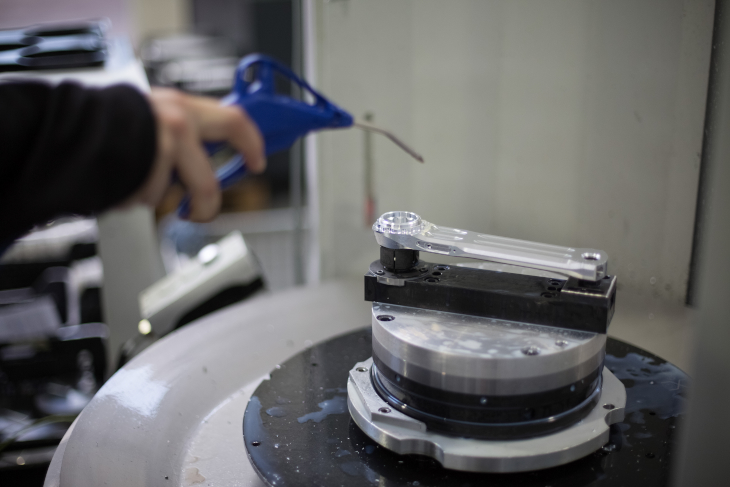
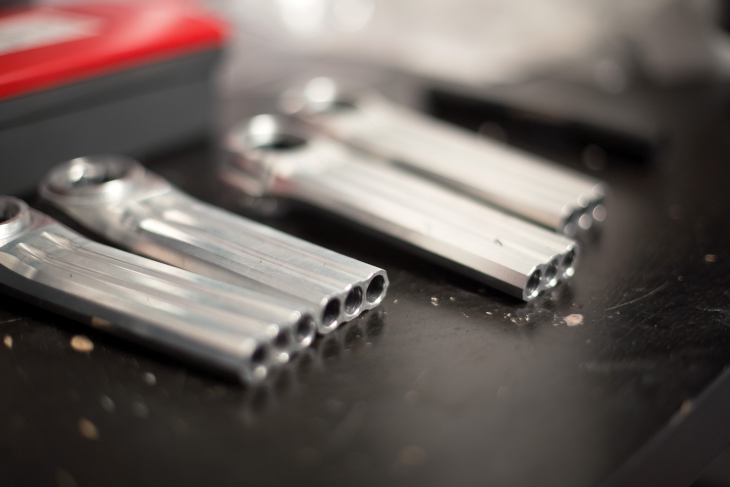
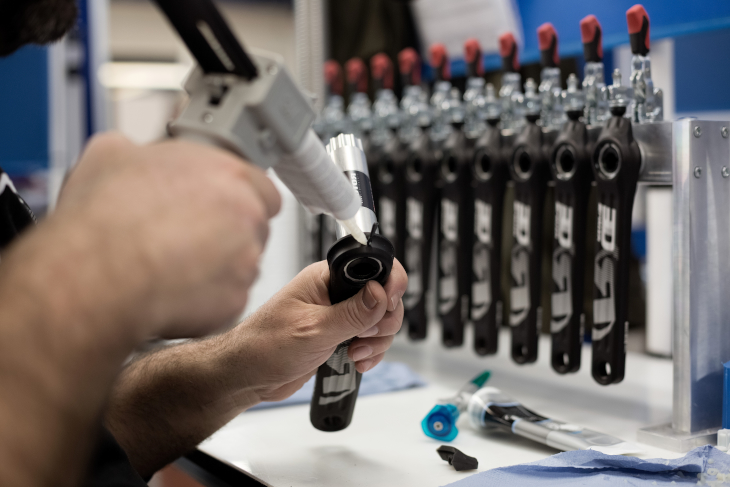
スパイダー部の工程も大まかな流れは共通。最後に、スピンドルを合わせた3点を組み立てることで、クランクは完成となる。なおアーム、スパイダー、スピンドルの3点はそれぞれ適材適所で合金種が変更されており、7075や6066などを組み合わせている。
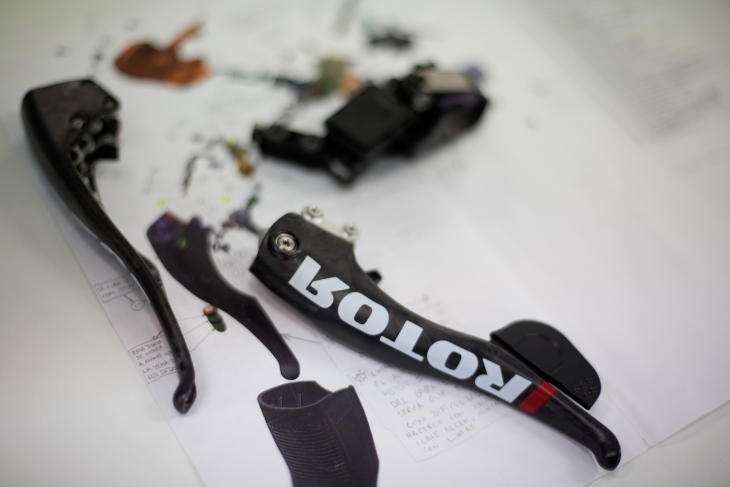
この熱可塑性カーボンを数枚重ねたものを120℃に熱し、150Barもの高い圧力で型に押し当てることでUNOのブレーキレバーは成型されている。素材の質感を見るに恐らく、UNOのリアディレーラーもプーリーゲージと同じ製法で成型されているようだ。
こうしてスペイン・マドリードで製造され、日本を始めとした世界38カ国に届けられるローターのプロダクツ。Q-Ringsや3Dクランク、UNOが如何にして生み出されるかを、読者の皆さんが少しでも理解して頂き、これまでより少しでも興味が沸いたなら幸いである。
レポート:山本雄哉(シクロワイアード編集部) 提供:ダイアテック