4月14日から6日間、イタリア・ミラノにて開催された国際家具見本市、通称「ミラノサローネ」で一台の自転車が発表された。「DFM01 OUSIA」と名付けられたそのバイクは、3Dプリンターで製作されたという。自転車界隈を超えて世間の耳目を集めるバイクの開発者が語る3Dプリンター、インダストリアルデザイン、そしてロードバイクの未来。
DFM01 OUSIA
3Dプリンターで出力された自転車。なんともキャッチ―な響きで、それだけでも十分な話題性があるはずだ。しかし、4月14日、イタリア・ミラノにて発表された「DFM01 OUSIA」と名付けられたバイクはそこにとどまることを良しとしなかった。
フレーム重量1kg、UCI規格に適合し、レースにも耐えうる十分な強度と剛性を兼ね備えた「実用競技車両」として製作されたという「DFM01 OUSIA」は驚きをもって迎えられ、世界中のメディアで取り上げられた。日本のSNS界隈でも盛り上がっており、どこかでそのデザインを目にした人は多いのではないだろうか。
このバイクのアイコンともいえるポリゴンチックなデザインのヘッドチューブ
インテグラルシートピラーを採用し、シートクランプは廃されている
チェーンステイは反応性を重視してフルチタンとされている
シートステーは細身のカーボンチューブ
そして、更に驚くべきはデザイン・製作を行ったのが日本人のプロジェクトチームによるものだったということ。iFデザイン賞の受賞経験のあるインダストリアルデザイナー、柳澤郷司氏の主宰するデザインスタジオ「Triple Bottom Line」が設計の中核を担い、川本尚毅氏率いる「N&R Folding Japan」が特徴的なポリゴンライクのデザインを施した。そして、DMM.comが秋葉原に設置したものづくり支援施設「DMM.make AKIBA」にて、実際の製品の試作および製作を行ったという。つまり、設計から生産に至るまで純国産のロードバイクなのだ。
そんな「DFM01 OUSIA」のデザインを手掛けた「Triple Bottom Line」の代表である柳澤氏に、DMM.make AKIBAにてインタビューする機会を得た。ミラノ・サローネでの発表から半月、輪界を飛び出して広く話題を集めるホットなプロダクトの裏側にあったストーリーをお届けしよう。
――まずはこのバイクのコンセプトについて教えてください
色々な資料を見せながら開発について語ってくれた柳澤氏
設計図面に線として落としこまれることで、さまざまな規格との整合性を確実に取ることができる 柳澤:「DFM01 OUSIA」は「Direct Fabrication Method」つまり、「消費者と製作者をよりダイレクトに繋ぐための生産手法」によるプロダクトの初号機として製作しました。今、3Dプリンターをはじめとしたデジタルファブリケーションやアディティブ・マニュファクチャリングが話題になっていますよね?でも、強度や精度の問題があって試作品やモックの製作には良いけど、実用品はちょっと……という風潮があると思います。
でも、そうじゃないんだよと。それらの生産手法でも、実用に耐えうる品質の製品を作ることができるということの実証機としてこのプロジェクトを動かしています。実際、僕たちが自前で生産プロセスを組み上げて、最初に作り上げたモデルがUCIの定める最下限重量からわずか200gだけ重い、7kgに収まったのには関わったみんなが驚いていました(笑)
――なるほど、そのテーマの中で自転車という題材を選んだ理由とは?
柳澤:自転車というのは程よくチャレンジしがいのある題材だったということです。人力がパワーリソースなので、効率化を図らないといけないし、UCIによってレギュレーションも定められています。まだまだ発展させていく余地も残されていますし、前々から自転車をデザインしたいという思いはあったんです。もちろん、自分が自転車が好きだということが大きいんですけど(笑)
――3Dプリンターで作られているという点に対して懐疑的な声も有りますが
柳澤:実際のところ、そういったイメージに対するアンチテーゼとしてのプロジェクトなんです。この企画が始まったのもDMM.make AKIBAさんから、デジタルファブリケーションを用いて面白いことができないのか?という相談があったからなんですよ。
乱暴な言い方ですが、それなりのスペックのパソコンと3Dプリンタがあればかなりのレベルで実用品が作れるんだ、という象徴的な例が出来ないかという話が持ち上がって。海外だと洋服作ったよ!とかシティサイクル作ったよ!というようないろいろな事例があるわけです。
実はその話が来た当初、僕は反対したんです(笑)3Dプリンターのような技術的素養が溜まっていない、ぽっと出の技術で実用品を製作することは出来ないと。確かにカタチだけをそれっぽく作ることはできるけれど、そんなものに何か意味があるのか?と考えていたんですよ。
金属や高分子化学材料といった素材学を研究していた私たちのようなインダストリアルデザイナーが関わる以上、安定した品質できちんと量産できて初めて実用と呼べる。職人が手間をかけて、一品ものを作り出すようなのは嗜好品、贅沢品の部類です。しかも3Dプリンターなんて嗜好品になるのかすらも危ういじゃないですか。
――その最初の反対を翻すことになったきっかけはなんだったのでしょうか?
アキバのものづくり支援施設「DMM.make AKIBA」ここでOusiaは生まれた
最初の試作ラグは約600gとかなりの重量級だった
治具ももちろんオリジナルだ 柳澤:その当時の私も3Dプリンターの最先端の状況について詳細を把握していたわけではなかったんです。ですので、2か月に渡って様々な業界にリサーチをかけてみたところ、どうやらイメージしていたよりもかなり実用レベルに近づいているということが確認できたんです。
たとえば、ボーイング787の非常扉のヒンジや、医療分野では人工関節といったものが3Dプリンターで作られているということですね。基幹技術となるものはできつつあるので、これならいけるでしょうということで、設計に入ることとなりました。
――なるほど、設計にあたって苦労した点などはあるのでしょうか?
柳澤:いや、もうホントに大変でしたよ!自転車業界というのは究極のクローズドコミュニティなんだな、と痛感しました(笑)
――つ、つまり?
柳澤:そうですね、各社がバラバラの規格で、それらの組み合わせでどれが正常に動くのか、というデータが全く無いところから設計を始める必要があった、ということです。たとえばボトムブラケットの規格でもJIS、ITA、BB30、プレスフィットなどたくさんあるわけですが、それに対して、チェーンラインが適切に取れるかどうか、どれだけチェーンステーが太いとチェーンが干渉する、といったような資料がどこを探しても無い(笑)
これは困ったぞ、となりまして、全ての規格を洗い出し、正常に動作するか否かのマトリクスを作るところから始めました。最終的には「この線の範囲の中で設計すれば問題ない」という形で図面に落とし込むことで、設計の土台を完成させました。
そこから先は、N&R Folding Japanの川本尚毅さんにミラノのピザと引き換えに特徴的な意匠を施していただいて、OUSIAは出来上がったというわけです。
DFM01 Ousia 生まれ故郷のアキバにて
――あのポリゴンライクな意匠にはどういった意味があるのですか?
柳澤:三角形というのは平面を構成する最小単位なので、一点を動かすことで自由に変形させることができるんです。現在、身長や足の長さといったデーターを入力することで最適なジオメトリを生成するソフトウェアを開発しています。あのデザインなら、容易にそのジオメトリに即した形状を出力することができるということですね。
個々人に合わせたオーダーメイドなものづくりができる、そして工業製品として信頼のおける均一なクオリティを両立するということが、このバイクの基本的な考え方でもあります。既存のマスプロフレームとビルダーによるオーダーフレームとの間を埋めるような存在があれば、それは新たな価値を生み出すことが出来るのではないかなと思っています。
――3Dプリンターで出力したラグ部分で新たな試みをされた点などはありますか?
柳澤:3Dプリンターで出力した金属パーツを実用品に使用するということ自体が新しい試みと言えますね。MITやGEの研究所の中でもかなりホットな分野なんです。なので、工作精度の確保や工業規格との整合性といったデータもほとんどなく、一つ変更を加えるたびにチェックをしながら進んでいくような手探りの状況でした。
また、これまで焼結したチタンは磨けないといわれていたんですが、今回のバイク製作にあたってMipox株式会の方と共に新しい研磨方法を見つけることで、表材に使えるだけのクオリティを持たせることが出来ました。プリントアウトしてから5分くらいの行程で磨きをかけることができ、コストも非常に抑えられます。こういった加工も、手作業ではなく機械化、自動化できるような方法で施工しています。
DMM.make AKIBAにてプレ発表会が行われた
内ラグ方式を採用することでバテッドチューブの様な効果を生み出している
こういった大規模な生産設備が用意されている
楕円形状のトップチューブ
――なるほど、カーボンチューブについてこだわりはあるのでしょうか?
柳澤:トップチューブは丸チューブは嫌で、長円か楕円形状にしたかったんですよ。でも、出来るだけ金型をはじめとした大掛かりな設備の使用を避けることがこのバイクのテーマでもあるので、新しく型を起こしてもらうことなくそういった形状のチューブを作れるメーカーさんとなるとかなり少なくって(笑)。
最終的には、滋賀にあるホーペックという会社にお願いすることになりました。マグロ遠洋漁業の釣り竿や人力飛行機の翼のカーボン桁などを手掛けているところで、先ほどの形状をはじめ、繊維の角度や強度の出し方など、いろいろな細かい注文にも対応してもらえました。
――なぜ発表の場として「ミラノ・サローネ」に選んだのでしょうか
AKB48劇場の前にたたずむ 柳澤:このバイクをNAHBSやBespokeで発表するというのは、あまりにも予定調和すぎるじゃないですか(笑)ミラノ・サローネはもちろん家具がメインの見本市なのですが、それ以上にデザインの祭典という側面もあります。そのなかでも、モビリティというカテゴリはかなり注目を集める存在になっているんですね。
私たちのほかにも、マツダさんが自転車を出展していたり、ルックやタイムといったバイクブランドも参加しています。ですので、自転車を展示するということに関しての違和感は全くありません。そして、こういった場で発表することによって、どうやって作ったのか?ということや、このデザインや製造手法を他分野にどうやって応用できるのか?ということに興味を抱いてもらえると思ったんです。
――なるほど、確かに自転車専門の展示会よりも、広い範囲で話題を呼んでいたように感じました。量産を目指したデザインということでしたが、販売など、今後の予定を教えていただけますか?
柳澤:今後は市販化に向けて動いていきたいと思っています。そのために、色々な欠点をつぶしたバージョンを設計しているところですね。実際にCAE解析をしてみると応力が分散していない箇所が残っていて。金属自体の限界点を越えなければ問題は無いはずなのですが、その知見がたまっていないので実際のところは何とも言えないんです。そのために振動試験などをこれから行っていくつもりですが、まだ1台しかないので壊せないので慎重にテストしていきます(笑)
開発に関わったメンバー達
加えて、パーソナライズされたマスプロダクション品質のロードバイクというコンセプトを推し進めていくつもりです。具体的には各種のセンサーやモジュールを内蔵することで、サイクリストが自転車に乗っている時に何が起きているのかをリアルタイムに、かつ有機的に把握できるシステムを構築するということですね。つまり、かかりが良いというのはどういうことなのか、しなりが推進力に変換されるというのはどういう現象なのか。それらを理解することで、ジオメトリーだけではなくバイク全体のライディングフィールを個人の好みへと近づけていくための試みです。
これらの取り組みを形にした「DFM02 Stoicheia」の開発は現在進行中で、今年の9月に発表を予定しております。ぜひご期待ください。
今までに前例の無いチャレンジの末に生まれたDFM01 OUSIA、読者の皆様にはどう響いただろうか。実際に会場前で軽く試乗させて頂いたのだが、固いバネ感のあるしっかりした乗り味で、不安や柔らかすぎるという印象は皆無だった。まだ試行錯誤が続いている状態でこそあるものの、競技用としての資質も万全だろう。
取材を通して感じたのは、「個」に向けてのカスタムメイドの新しい時代。自転車としてはもちろん、他の工業分野においても画期的な前例となるのではないのだろうか?ということだ。これこそが、今を行く「日本のモノづくり」の新しいステージなのだ。
text:Naoki.YASUOKA
photo:So.Isobe
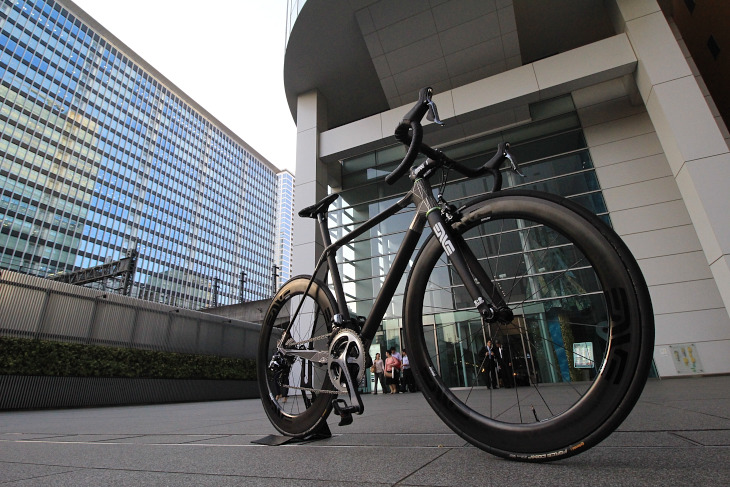
3Dプリンターで出力された自転車。なんともキャッチ―な響きで、それだけでも十分な話題性があるはずだ。しかし、4月14日、イタリア・ミラノにて発表された「DFM01 OUSIA」と名付けられたバイクはそこにとどまることを良しとしなかった。
フレーム重量1kg、UCI規格に適合し、レースにも耐えうる十分な強度と剛性を兼ね備えた「実用競技車両」として製作されたという「DFM01 OUSIA」は驚きをもって迎えられ、世界中のメディアで取り上げられた。日本のSNS界隈でも盛り上がっており、どこかでそのデザインを目にした人は多いのではないだろうか。
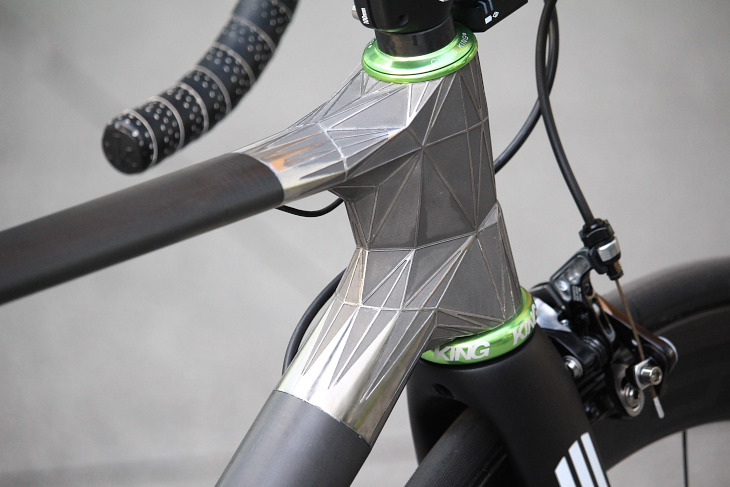
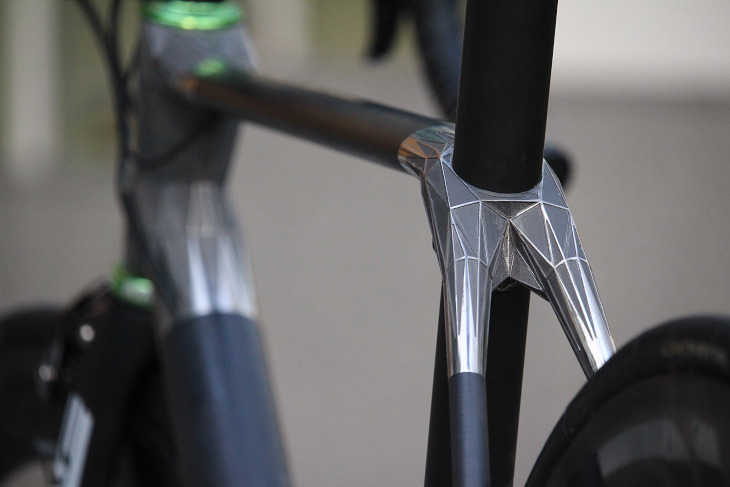
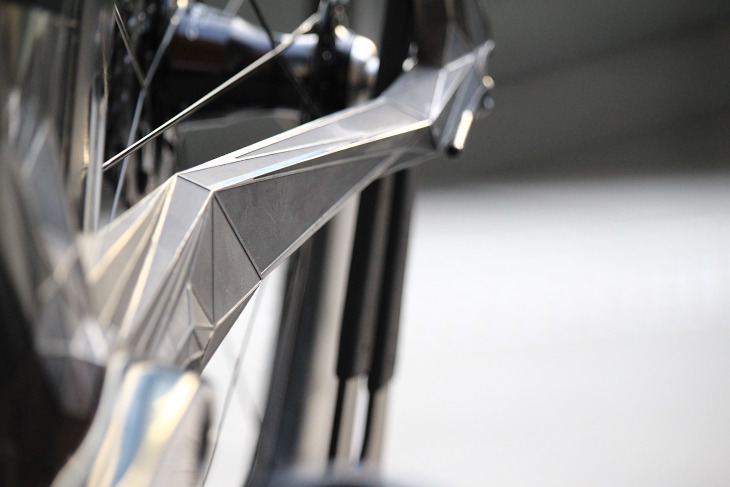
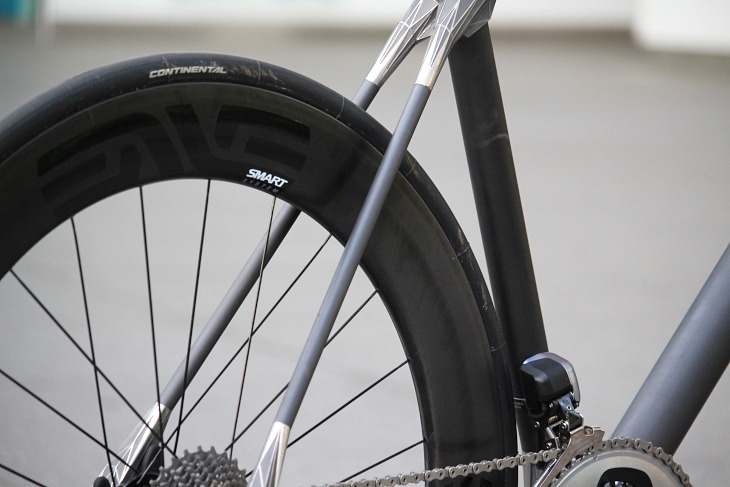
そして、更に驚くべきはデザイン・製作を行ったのが日本人のプロジェクトチームによるものだったということ。iFデザイン賞の受賞経験のあるインダストリアルデザイナー、柳澤郷司氏の主宰するデザインスタジオ「Triple Bottom Line」が設計の中核を担い、川本尚毅氏率いる「N&R Folding Japan」が特徴的なポリゴンライクのデザインを施した。そして、DMM.comが秋葉原に設置したものづくり支援施設「DMM.make AKIBA」にて、実際の製品の試作および製作を行ったという。つまり、設計から生産に至るまで純国産のロードバイクなのだ。
そんな「DFM01 OUSIA」のデザインを手掛けた「Triple Bottom Line」の代表である柳澤氏に、DMM.make AKIBAにてインタビューする機会を得た。ミラノ・サローネでの発表から半月、輪界を飛び出して広く話題を集めるホットなプロダクトの裏側にあったストーリーをお届けしよう。
――まずはこのバイクのコンセプトについて教えてください
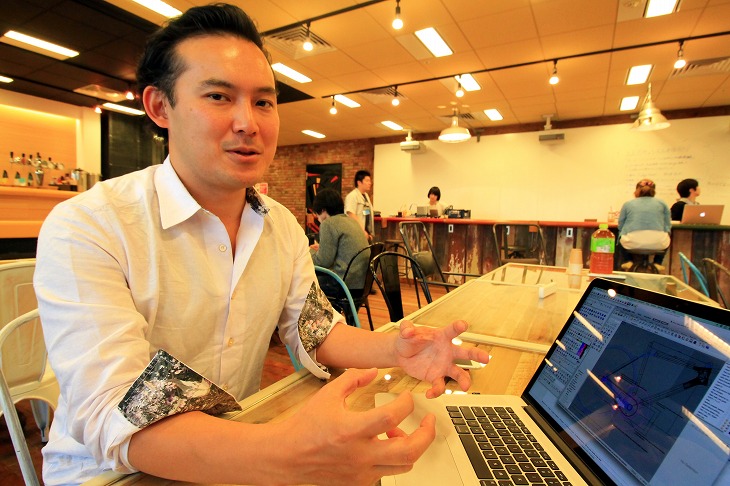
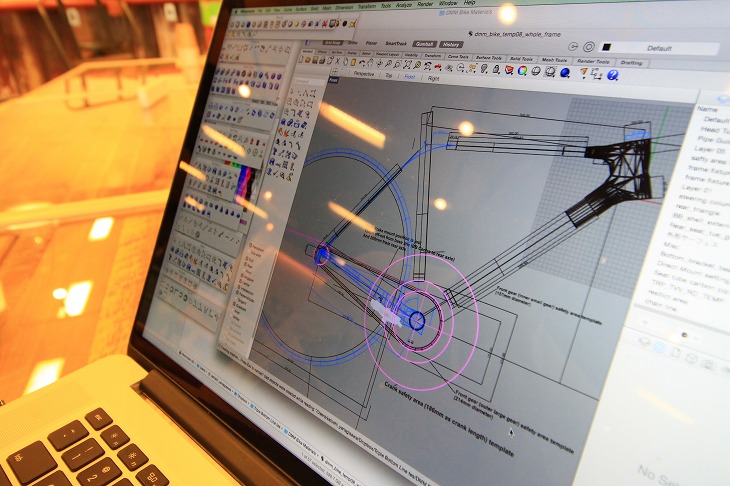
でも、そうじゃないんだよと。それらの生産手法でも、実用に耐えうる品質の製品を作ることができるということの実証機としてこのプロジェクトを動かしています。実際、僕たちが自前で生産プロセスを組み上げて、最初に作り上げたモデルがUCIの定める最下限重量からわずか200gだけ重い、7kgに収まったのには関わったみんなが驚いていました(笑)
――なるほど、そのテーマの中で自転車という題材を選んだ理由とは?
柳澤:自転車というのは程よくチャレンジしがいのある題材だったということです。人力がパワーリソースなので、効率化を図らないといけないし、UCIによってレギュレーションも定められています。まだまだ発展させていく余地も残されていますし、前々から自転車をデザインしたいという思いはあったんです。もちろん、自分が自転車が好きだということが大きいんですけど(笑)
――3Dプリンターで作られているという点に対して懐疑的な声も有りますが
柳澤:実際のところ、そういったイメージに対するアンチテーゼとしてのプロジェクトなんです。この企画が始まったのもDMM.make AKIBAさんから、デジタルファブリケーションを用いて面白いことができないのか?という相談があったからなんですよ。
乱暴な言い方ですが、それなりのスペックのパソコンと3Dプリンタがあればかなりのレベルで実用品が作れるんだ、という象徴的な例が出来ないかという話が持ち上がって。海外だと洋服作ったよ!とかシティサイクル作ったよ!というようないろいろな事例があるわけです。
実はその話が来た当初、僕は反対したんです(笑)3Dプリンターのような技術的素養が溜まっていない、ぽっと出の技術で実用品を製作することは出来ないと。確かにカタチだけをそれっぽく作ることはできるけれど、そんなものに何か意味があるのか?と考えていたんですよ。
金属や高分子化学材料といった素材学を研究していた私たちのようなインダストリアルデザイナーが関わる以上、安定した品質できちんと量産できて初めて実用と呼べる。職人が手間をかけて、一品ものを作り出すようなのは嗜好品、贅沢品の部類です。しかも3Dプリンターなんて嗜好品になるのかすらも危ういじゃないですか。
――その最初の反対を翻すことになったきっかけはなんだったのでしょうか?
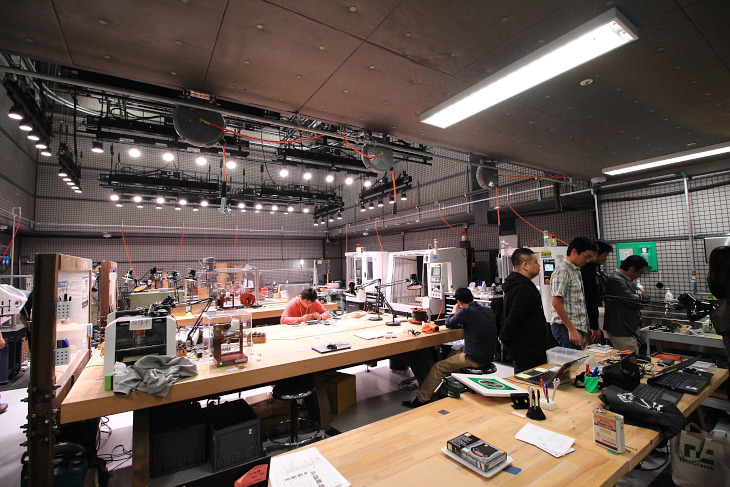
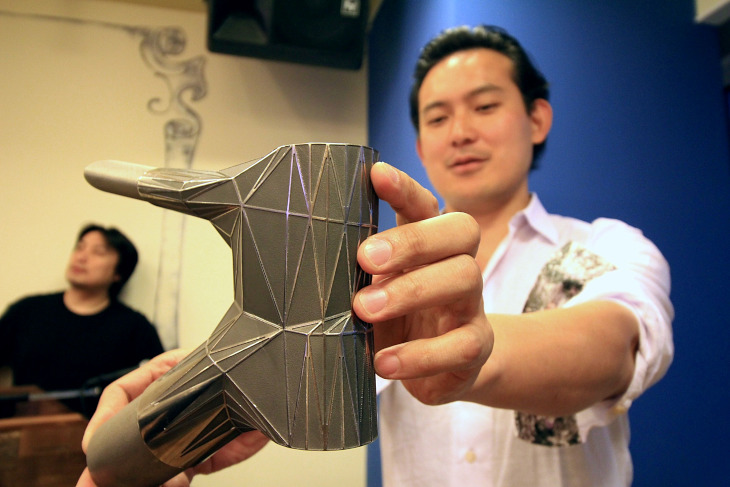
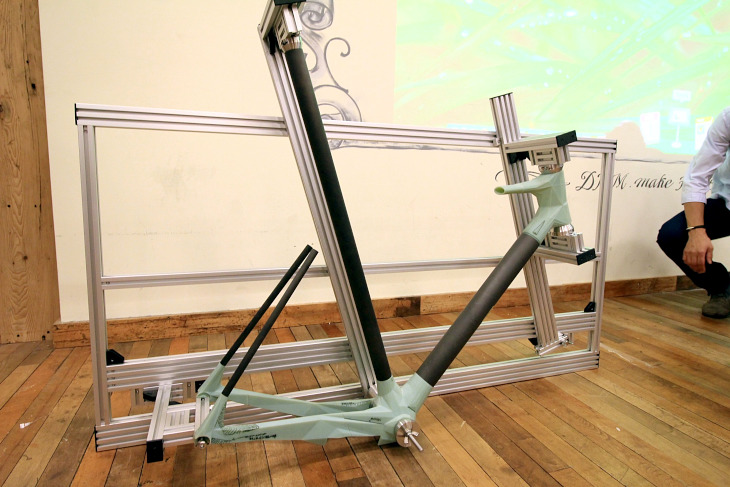
たとえば、ボーイング787の非常扉のヒンジや、医療分野では人工関節といったものが3Dプリンターで作られているということですね。基幹技術となるものはできつつあるので、これならいけるでしょうということで、設計に入ることとなりました。
――なるほど、設計にあたって苦労した点などはあるのでしょうか?
柳澤:いや、もうホントに大変でしたよ!自転車業界というのは究極のクローズドコミュニティなんだな、と痛感しました(笑)
――つ、つまり?
柳澤:そうですね、各社がバラバラの規格で、それらの組み合わせでどれが正常に動くのか、というデータが全く無いところから設計を始める必要があった、ということです。たとえばボトムブラケットの規格でもJIS、ITA、BB30、プレスフィットなどたくさんあるわけですが、それに対して、チェーンラインが適切に取れるかどうか、どれだけチェーンステーが太いとチェーンが干渉する、といったような資料がどこを探しても無い(笑)
これは困ったぞ、となりまして、全ての規格を洗い出し、正常に動作するか否かのマトリクスを作るところから始めました。最終的には「この線の範囲の中で設計すれば問題ない」という形で図面に落とし込むことで、設計の土台を完成させました。
そこから先は、N&R Folding Japanの川本尚毅さんにミラノのピザと引き換えに特徴的な意匠を施していただいて、OUSIAは出来上がったというわけです。
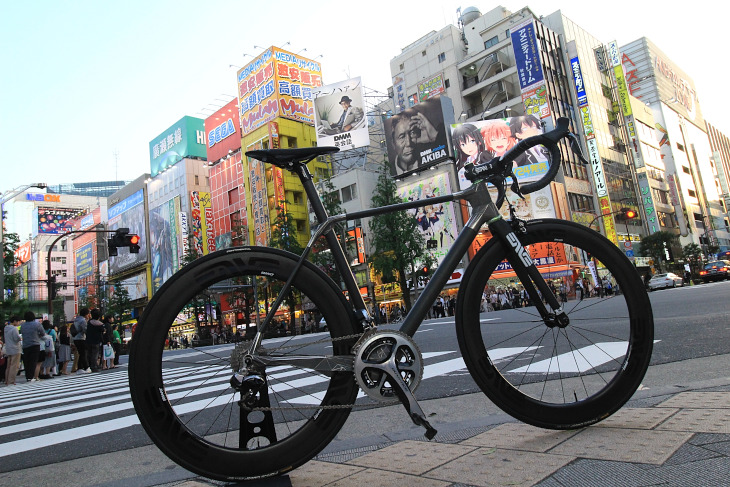
――あのポリゴンライクな意匠にはどういった意味があるのですか?
柳澤:三角形というのは平面を構成する最小単位なので、一点を動かすことで自由に変形させることができるんです。現在、身長や足の長さといったデーターを入力することで最適なジオメトリを生成するソフトウェアを開発しています。あのデザインなら、容易にそのジオメトリに即した形状を出力することができるということですね。
個々人に合わせたオーダーメイドなものづくりができる、そして工業製品として信頼のおける均一なクオリティを両立するということが、このバイクの基本的な考え方でもあります。既存のマスプロフレームとビルダーによるオーダーフレームとの間を埋めるような存在があれば、それは新たな価値を生み出すことが出来るのではないかなと思っています。
――3Dプリンターで出力したラグ部分で新たな試みをされた点などはありますか?
柳澤:3Dプリンターで出力した金属パーツを実用品に使用するということ自体が新しい試みと言えますね。MITやGEの研究所の中でもかなりホットな分野なんです。なので、工作精度の確保や工業規格との整合性といったデータもほとんどなく、一つ変更を加えるたびにチェックをしながら進んでいくような手探りの状況でした。
また、これまで焼結したチタンは磨けないといわれていたんですが、今回のバイク製作にあたってMipox株式会の方と共に新しい研磨方法を見つけることで、表材に使えるだけのクオリティを持たせることが出来ました。プリントアウトしてから5分くらいの行程で磨きをかけることができ、コストも非常に抑えられます。こういった加工も、手作業ではなく機械化、自動化できるような方法で施工しています。
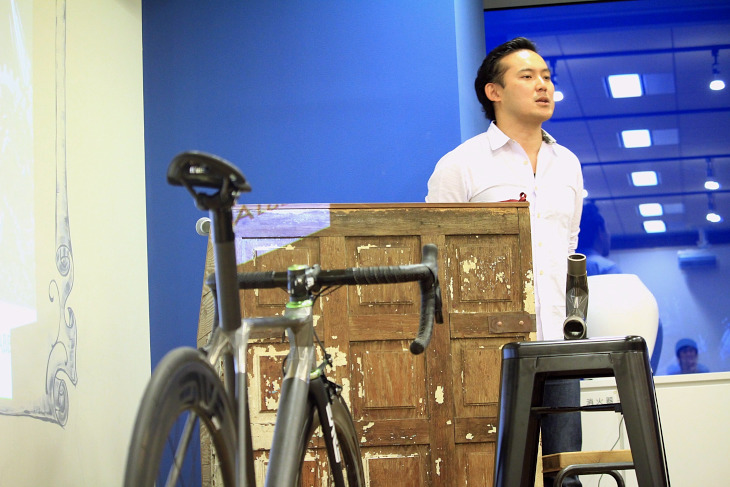
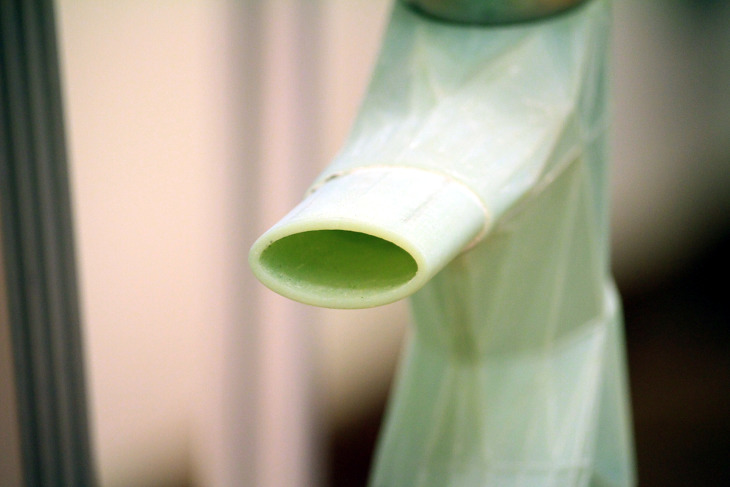

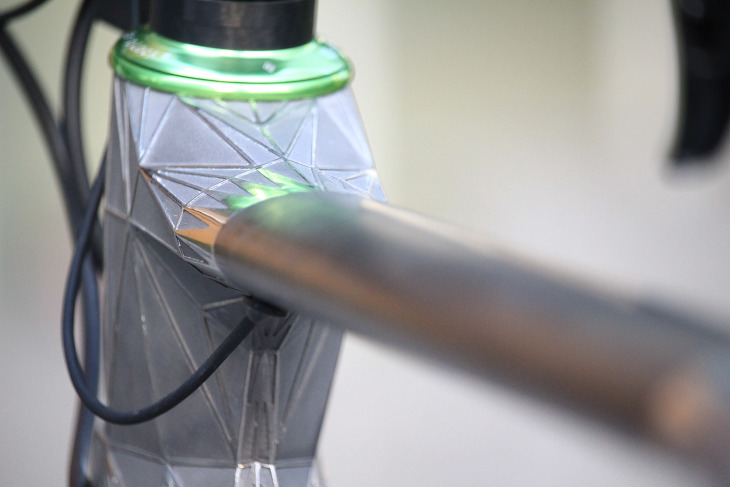
――なるほど、カーボンチューブについてこだわりはあるのでしょうか?
柳澤:トップチューブは丸チューブは嫌で、長円か楕円形状にしたかったんですよ。でも、出来るだけ金型をはじめとした大掛かりな設備の使用を避けることがこのバイクのテーマでもあるので、新しく型を起こしてもらうことなくそういった形状のチューブを作れるメーカーさんとなるとかなり少なくって(笑)。
最終的には、滋賀にあるホーペックという会社にお願いすることになりました。マグロ遠洋漁業の釣り竿や人力飛行機の翼のカーボン桁などを手掛けているところで、先ほどの形状をはじめ、繊維の角度や強度の出し方など、いろいろな細かい注文にも対応してもらえました。
――なぜ発表の場として「ミラノ・サローネ」に選んだのでしょうか
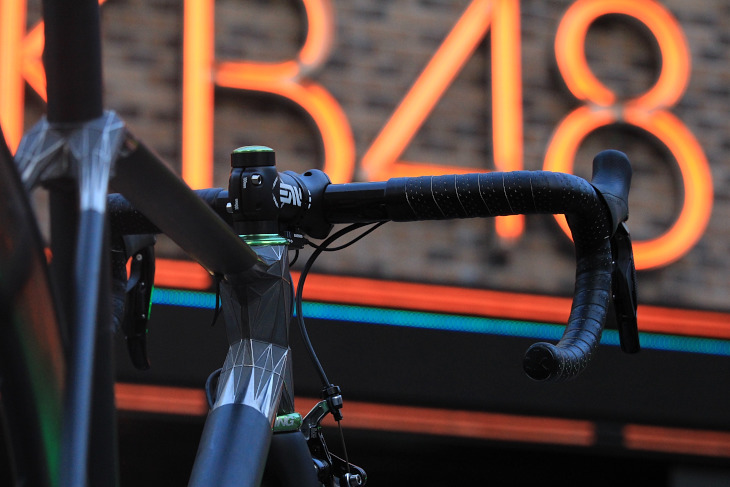
私たちのほかにも、マツダさんが自転車を出展していたり、ルックやタイムといったバイクブランドも参加しています。ですので、自転車を展示するということに関しての違和感は全くありません。そして、こういった場で発表することによって、どうやって作ったのか?ということや、このデザインや製造手法を他分野にどうやって応用できるのか?ということに興味を抱いてもらえると思ったんです。
――なるほど、確かに自転車専門の展示会よりも、広い範囲で話題を呼んでいたように感じました。量産を目指したデザインということでしたが、販売など、今後の予定を教えていただけますか?
柳澤:今後は市販化に向けて動いていきたいと思っています。そのために、色々な欠点をつぶしたバージョンを設計しているところですね。実際にCAE解析をしてみると応力が分散していない箇所が残っていて。金属自体の限界点を越えなければ問題は無いはずなのですが、その知見がたまっていないので実際のところは何とも言えないんです。そのために振動試験などをこれから行っていくつもりですが、まだ1台しかないので壊せないので慎重にテストしていきます(笑)
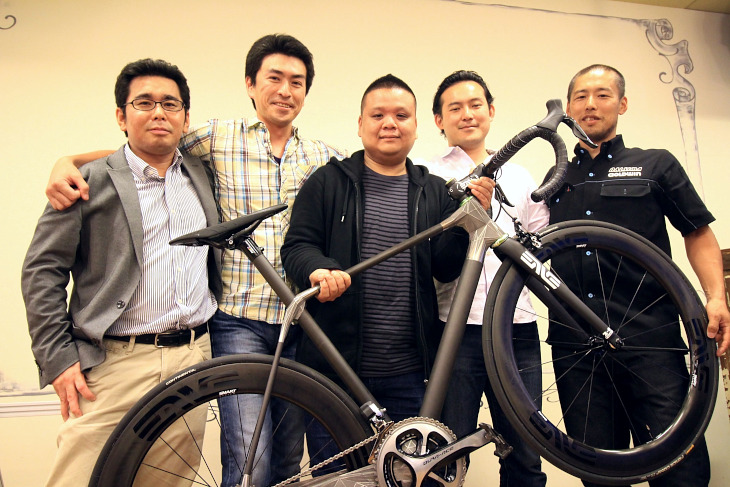
加えて、パーソナライズされたマスプロダクション品質のロードバイクというコンセプトを推し進めていくつもりです。具体的には各種のセンサーやモジュールを内蔵することで、サイクリストが自転車に乗っている時に何が起きているのかをリアルタイムに、かつ有機的に把握できるシステムを構築するということですね。つまり、かかりが良いというのはどういうことなのか、しなりが推進力に変換されるというのはどういう現象なのか。それらを理解することで、ジオメトリーだけではなくバイク全体のライディングフィールを個人の好みへと近づけていくための試みです。
これらの取り組みを形にした「DFM02 Stoicheia」の開発は現在進行中で、今年の9月に発表を予定しております。ぜひご期待ください。
今までに前例の無いチャレンジの末に生まれたDFM01 OUSIA、読者の皆様にはどう響いただろうか。実際に会場前で軽く試乗させて頂いたのだが、固いバネ感のあるしっかりした乗り味で、不安や柔らかすぎるという印象は皆無だった。まだ試行錯誤が続いている状態でこそあるものの、競技用としての資質も万全だろう。
取材を通して感じたのは、「個」に向けてのカスタムメイドの新しい時代。自転車としてはもちろん、他の工業分野においても画期的な前例となるのではないのだろうか?ということだ。これこそが、今を行く「日本のモノづくり」の新しいステージなのだ。
text:Naoki.YASUOKA
photo:So.Isobe
Amazon.co.jp